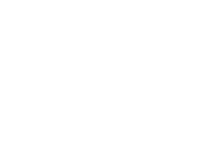 |
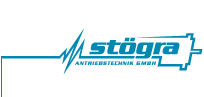 |
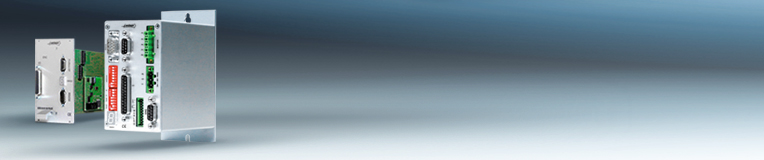 |
|
|
home
products
position
controls SERS overview |
|
|
|
|
SERS/WSERS overview |
|
|
|
|
|
|
|
|
|
|
|
Stepping motor positioning control for 2-phases-stepping
motors with RS232, RS485,
Profibus-DP or CANopen interface
and features as follows: |
|
|
|
|
|
flexible but easy programmable position control with
many special functions |
|
|
|
|
|
cost effective single or multiple axis control |
|
|
|
|
|
microstepping power amplifer with
12800 steps/revolution |
|
|
|
|
|
easy programmable via standard-windows-PC free
programming software for SERS/WSERS with RS232 interface |
|
|
|
|
|
Alternative programming and operation via hand programming
device
(4x16 character-display with 16-key membrane keyboard) |
|
|
|
|
|
eurocard-format for 19 inch 3HE systems for external
DC-supply
or complete panel mount or 19 inch rack systems
with integrated power supply (230VAC-50/60Hz) |
|
|
|
|
|
compact housing version
WSERS xx.80 and WSERS xx.230AC
with 4A or 8A for 20-80VDC supply
or 4A or 6A for direct mains supply (115VAC/230VAC-50/60Hz) |
|
|
|
|
|
flexible system due to modular design
including up to 3 axis 12A/phase with power supply
or 5 axis 12A/phase without power supply in one rack
or up to 6 axis 4,2A/phase with power supply
or 8 axis 4,2A/phase without power supply in one rack |
|
|
|
|
|
easy installation of the panel mount / 19 inch system
because of screw terminals / spring loaded terminals for all connections
like supply, motor, inputs, limit, home and stop switches |
|
|
|
|
|
|
|
The SERS is a point to point stepping motor
position control for 2-phases-stepping motors
The SERS is available in different versions with: |
|
|
|
| |
phase currents from 0 to14,5 A/phase (programable via
interface) |
|
|
|
|
|
power supply 24 VDC until 240 VDC |
|
|
|
|
|
optionally mains ready (230VAC 50Hz – optionally
also for 115 VAC 60Hz)
panel mount system or standard 3 height unit 19 inch system |
|
|
|
|
|
The SERS is controlled and programmed via a serial interface
(in standard version RS232C/V24).
Optionally there are versions with RS485, Profibus
DP, PROFIdrive
or CAN open interface
|
|
|
|
|
|
|
|
|
|
|
|
|
|
Operation modes: |
|
|
|
|
|
|
|
All operation modes are implemented in all standard SERS controls.
The operation mode is selected by setting parameters and the structure
of programming |
|
|
|
|
|
|
|
Serial mode |
|
|
|
|
|
|
|
 |
|
|
|
|
|
|
|
In the serial mode the SERS is controlled via the serial interface
by a PC, PLC or NC.
New positions (optionally with indication of velocity and acceleration,
in case these
values are changed) are sent via the serial interface and the SERS
is started by sending
an "execution" command. Inputs and outputs may be read and
set any time.
Also stored subroutines in the E²prom of the SERS may be called
and started via the
serial interface. By reading the corresponding parameters it can be
checked any time,
if the SERS is still buisy with executing a positioning job or a called
subroutine. |
|
|
|
|
|
|
|
Parallel / BCD mode |
|
|
|
|
|
|
|
 |
|
|
|
|
|
|
|
In this mode, different programms or just single commands are stored
into the E²prom
of the SERS. The stored programms/commands can be selected with up
to 7 digital inputs
(address lines) and be started by a start (strobe) signal. In that
way a PLC may select via
its digital outputs up to 128 different programs in a SERS. |
|
|
|
|
|
|
|
Master-Slave mode |
|
|
|
|
|
|
|
 |
|
|
|
|
|
|
|
2 or more SERS are connected via the RS232-interface. One of the
SERS is configured as MASTER,
the other SERS as SLAVES. The MASTER-SERS controls the SERS-SLAVES
via the serial interface.
The MASTER-SERS may send positioning jobs to the SLAVES and start
them and at the same time
execute a positioning job itself. Inputs and outputs of the SLAVES
can be requested and set.
The MASTER-SERS is able to start subroutines stored in the SERS-SLAVES
and may request the
status of the SERS-SLAVES. |
|
|
|
|
|
|
|
Standalone mode |
|
|
|
|
|
|
|
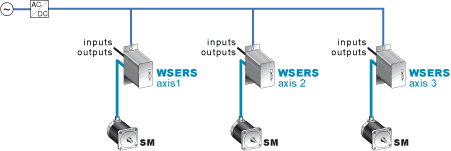 |
|
|
|
|
|
|
|
The SERS is operating independently of other controls or axis.
A stored operational program in the
E²prom of the SERS is executed after a program start signal at
an digital input or after power-on.
In the program defined positions and commands are executed one after
the other.
The running program may be programmed in a way, that it depends on
digital inputs, and outputs
may be set or reset. |
|
|
|
|
|
|
|
Manual mode |
|
|
|
|
|
|
|
The digital inputs can be defined as manual (jog) functions. When
activating the inputs,
the corresponding functions are executed. Following functions are
implemented: |
|
|
|
|
|
|
 |
jog slow left and right |
|
|
|
 |
jog fast left and right |
|
|
|
 |
homing procedure |
|
|
|
 |
motor current ON / Motor current OFF - reset errors / warnings |
|
|
|
 |
stop |
|
|
|
 |
start operational programm |
|
|
|
|
|
|
|
All manual functions are available also in the other operation
modes (e.g it can be defined
that in the serial mode jog slow functions are available at inputs
I1 and I2, and the other inputs
are free programmable) |
|
|
|
|
|
|
|
Download |
|
|
|
position control
SERS/WSERS and SERS Programmer 2
– single data sheet (641 KByte) |
|
|
|
stepping
motor controls catalogue 2015 –
catalogue (1838 KByte) |
|
|
|
|
stepper motors I
position controls I
power amplifiers I equipment
I home I info@stoegra.de |
|